Author |
Topic  |
Aaron Cake
Administrator
    
Canada
6718 Posts |
Posted - Jun 01 2005 : 09:03:41 AM
|
(Here's the latest on my RX-7 project. As last time, this is written primarily with RX-7 owners in mind, so some of the stuff here may need to be explained if you are not familiar with the car. Just ask...)
It's time once again for another update on my ongoing turbo-NA-bridgeport project. The previous thread in this series can be found here. Progress over the last few months has seemed slow due to not having large amounts of continuous time to work on things. But in reality, actually a lot has been accomplished. Many of these tasks are small, but in a project such as this, the meat of what needs to be done are small side jobs in between the large chunks. Thus, these pictures probably aren't anything ground breaking or as interesting as an engine assembly. Most of them deal with things outside the engine bay. While these aren't as glamorous as porting or engine assembly, they are necessary parts of the groundwork that supports the larger part of what is taking place.
That said, I don't think anyone will find this post boring. As always, there are a few neat details that you won't see anywhere else. All of this has brought me to what will take place very soon (not in this thread): after almost three years, the engine will be reinstalled in the car.
So, to pick up where we last left off, here's the lower intake after some quick porting. Since it was already being heavily modified, I figured that I might as well port it. The gains are very small, and it's absolutely not worth doing unless you already have the intake removed and are very bored.
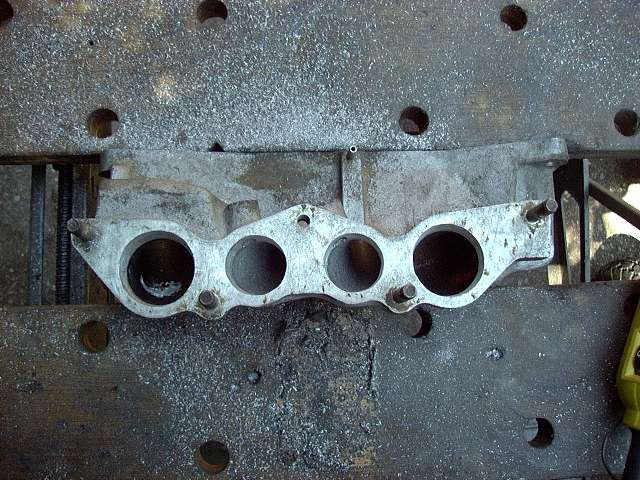
With the engine moved out of the basement and into the garage, it was time to install the oil pan. First, the oil pressure regulator was installed, and then the pickup. This oil regulator has been modified by shimming. Two M5 flat washers were placed inside the bottom of the piston. This increases spring tension, and thus oil pressure. Two washers should make for about 100 PSI of pressure.
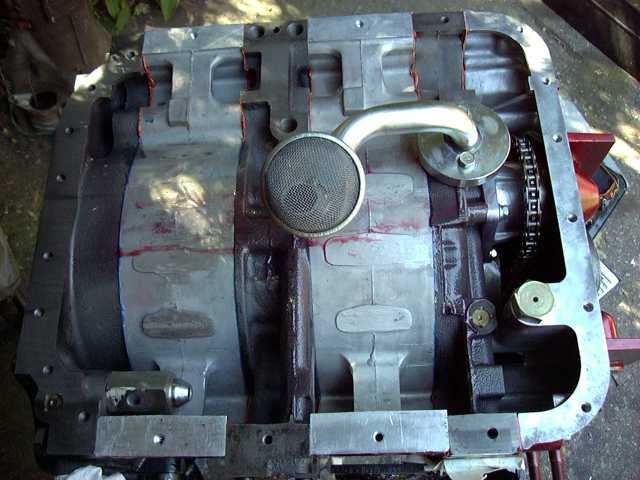
Next, the gasket and sealant were installed. On top of that, a Racing Beat baffle plate was installed. This plate prevents the oil from sloshing away from the pickup during deep, high speed turns. A must for anyone intending to autocross or track the car.
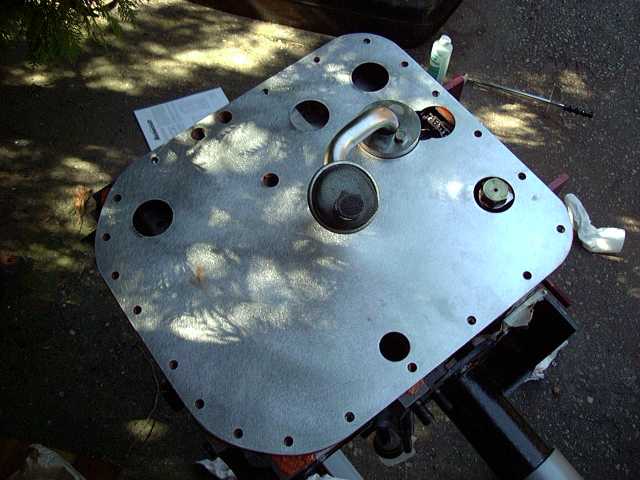
And then the oil pan is installed, with another gasket between it and the baffle. Notice the stainless steel bolts, as well as the wide washers. The washers help spread out the force from the bolt heads, thus going a long way to preventing oil leaks. I had to manually cut each of these bolts to size. Anytime stainless hardware is used, anti-seize MUST be applied to the threads. Otherwise, the stainless will weld itself to the aluminum of the engine.
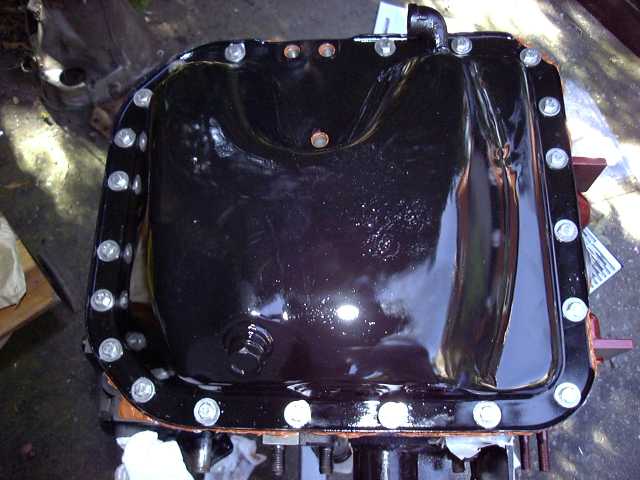
With the oil pan installed, it was time to do a little porting on the turbo wastegate.
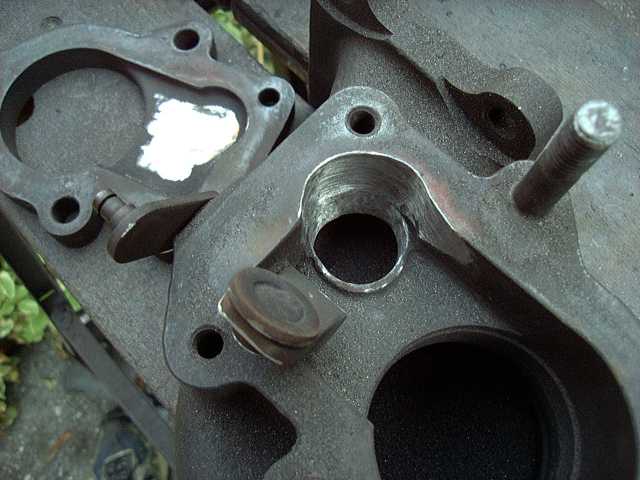
You can see how the wastegate orifice is becoming much larger then the flapper door itself. This is the ONLY way to effectively port the wastegate. Also, relief has been cut into the backing plate to allow the wastegate to swing open much wider.
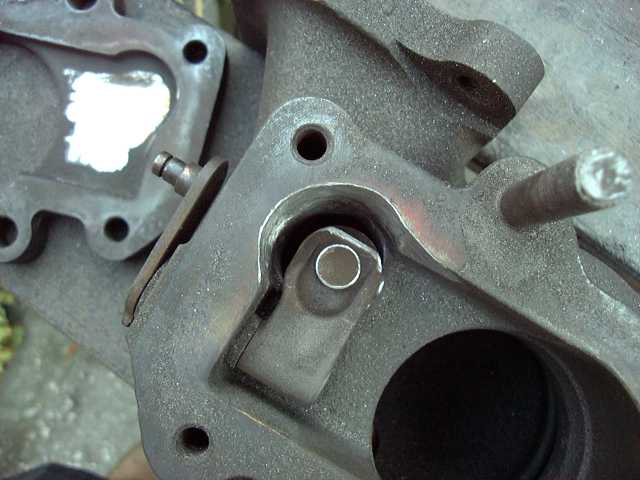
A very dark interior view of that wastegate.
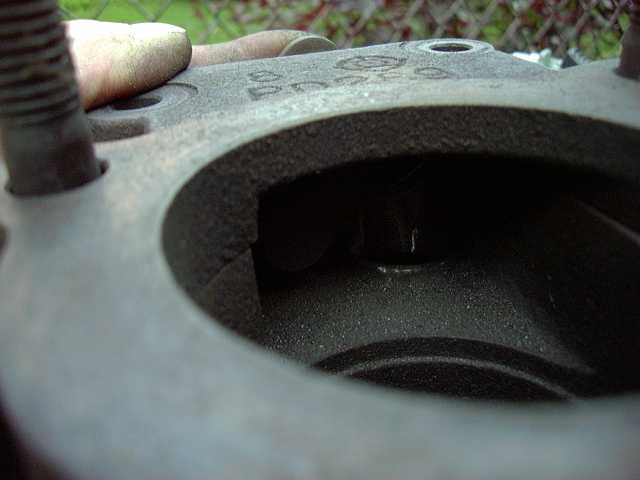
Since the turbo is disassembled, might as well port those exhaust runners. Here, you see the smaller twin-scroll runner is now ported as large as the "main" runner.

My clutch came about this time. Purchased from www.cpracing.ca" target="_blank">CP Racing. It's just a nice looking clutch. :) Also, much stronger then stock.
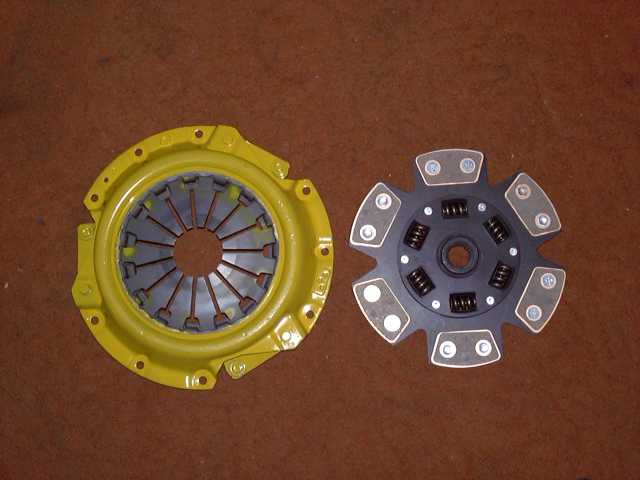
For a change, it's time to work inside the car. The carpets are being replaced, the door panels recovered, and the seats recovered. First step was to remove the carpet, seats and console.
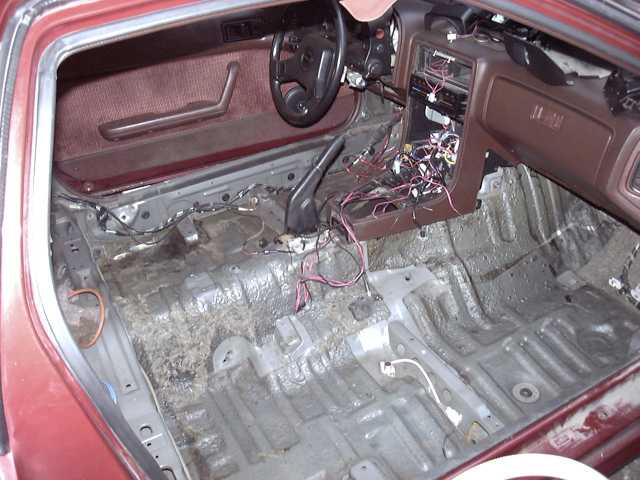
While pulling apart the storage bin areas, I made a horrible discovery: cancer! This was found on the drivers side.
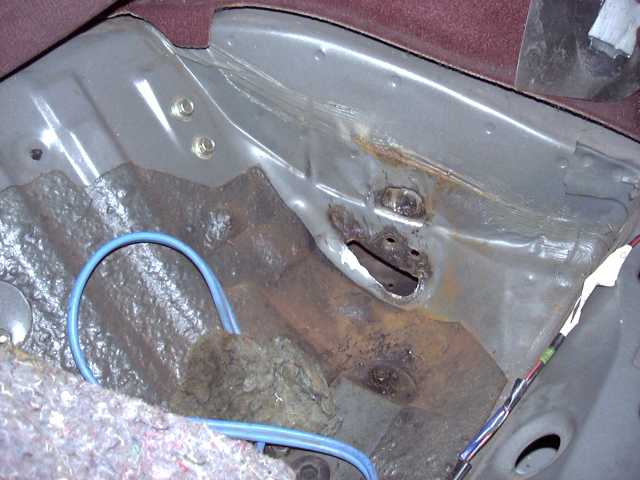
More on the passenger side. Clearly, the bolt holes for the rear seats have allowed moisture to get trapped between the frame rail and body in an unprotected area. So it rotted through.

A few other minor areas of concern were found. Any surface rust was ground off then primed to prevent further corrosion.
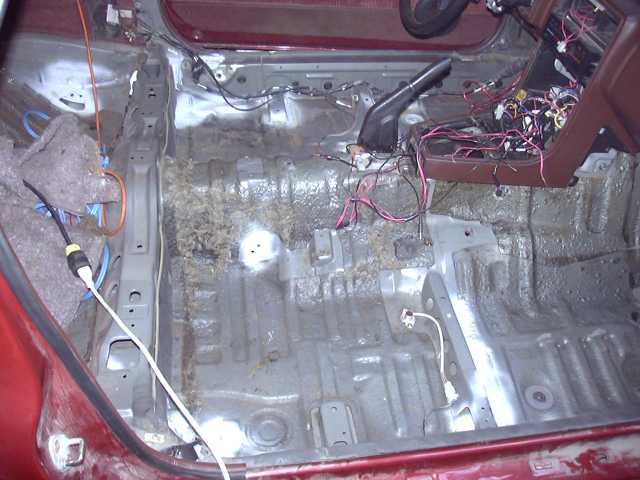
The only way to fight cancer is to cut it out. Rotted metal must be cut away to expose good metal, then a patch panel made and welded in. Below shows the large hole left after cutting the cancerous skin away, and the new panel of virgin steel.
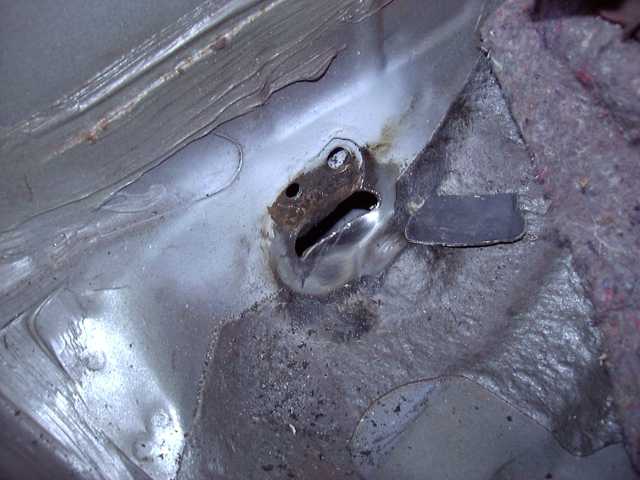
The new panel is welded in. Welding thin sheet metal takes patience, and a thin wire. Unfortunately, I only had 0.035" wire on hand, so there was some frustration involved.
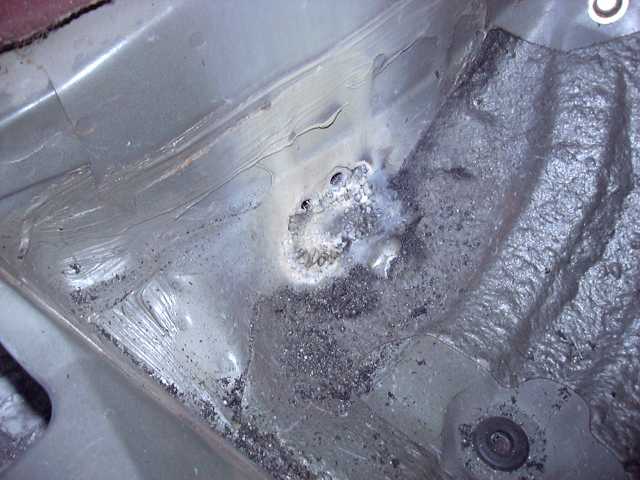

The welds are ground down. Truthfully, this area didn't have to be perfect, since it is going to be covered by a battery box. But it does have to be presentable.
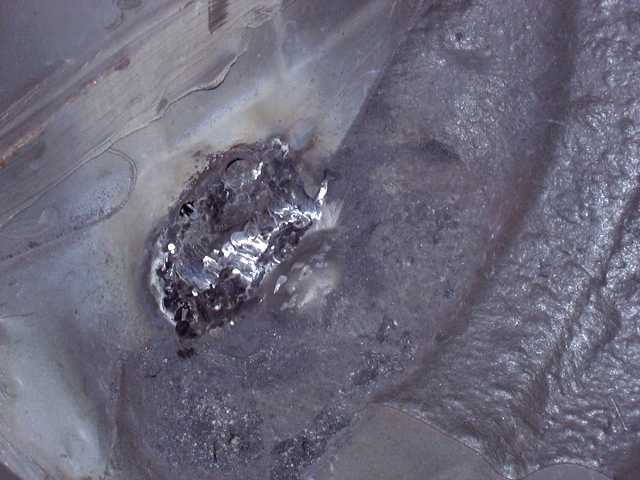
A similar panel was made for the driver side. The patch was actually quite a lot larger in that area. More care was taken on this side, since in theory, someone at some point might see it. But it doesn't need the effort necessary when working on a visible exterior panel. The black mark you see is actually the undercoating that made it's way through the bolt hole and oozed over the primer.
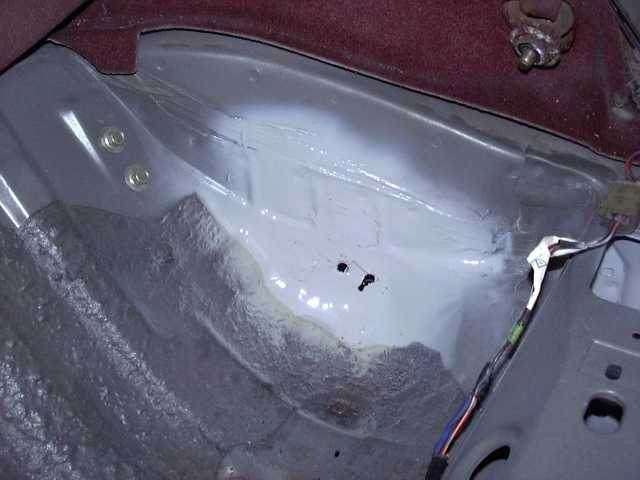
The passenger side patch is finished. A bolt was welded to the panel to provide a good ground for the battery. But this bolt is actually going to be removed since it's in the way of the battery box.
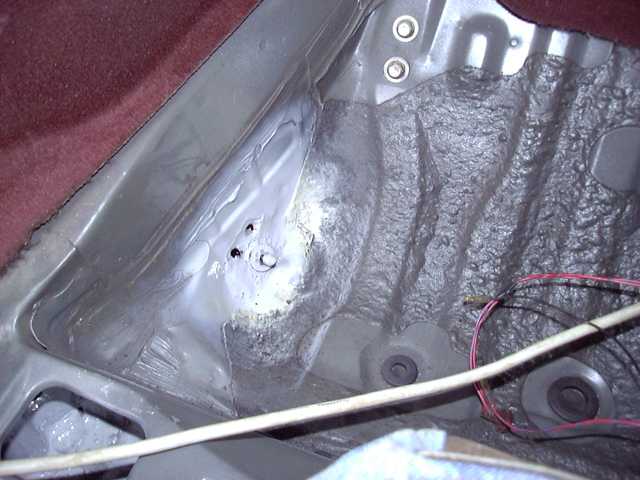
After the cancer treatments, the remaining interior touch ups were made and some of the wiring is being laid in place.
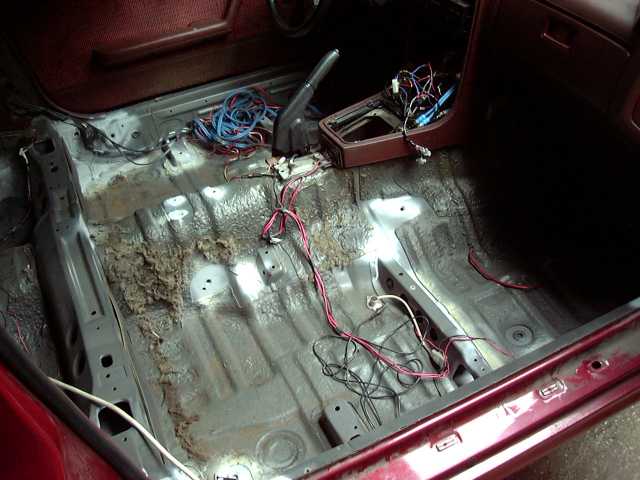
Since I am ditching the stock ECU in favor of the Microtech LT-8, most of the engine wiring harness is no longer needed. The only thing necessary to keep are the leads to the wiper motor, alternator and coolant sensor. On the right is what's left of the stock wiring harness. On the right is all the unneeded stuff. I was amazed at the condition my stock wiring harness was in. Underneath the crusty exterior, the inner wires looked as if they had just come from the factory. Goes to show you that the Mazda wiring, while somewhat unique, is high quality stuff.
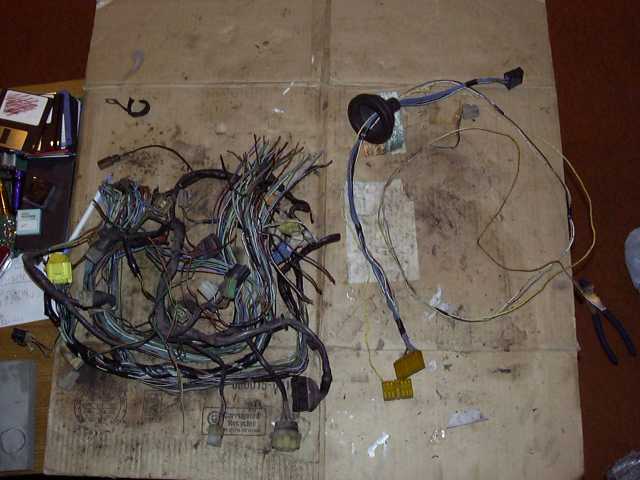
Wires were then run down the driver side sill for the audio and MP3 player. In this bundle, power for both the amp and MP3 player, speaker wires from the amp, signal wires to the amp, and audio to/from the MP3 player. Also a few other misc signal wires. Of course, this bundle tucks neatly underneath the fiberboard cover. It's a cardinal rule to never mix power and signal wires, but in this case, all the audio signal wires are heavily shielded, so there will be no problems.
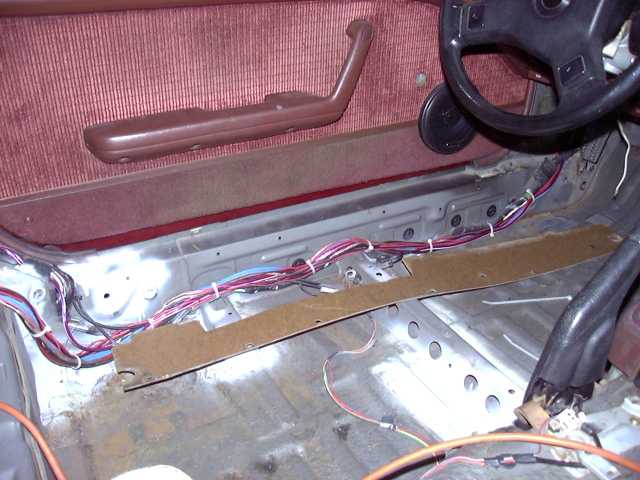
The passenger side wiring was done next. Shown here are the two thick (power and ground) battery cables, the rear passenger speaker wire, and the power and ground for the fuel pump. I prefer to ground my battery to multiple locations. This means running a large ground wire from the battery to the car in several places, and ultimately to the engine as well. Multiple GOOD grounds are vitally important. The fuel pump also has it's own separate ground, as will the ignition box and Microtech. This the only way to assure clean power to these important components.
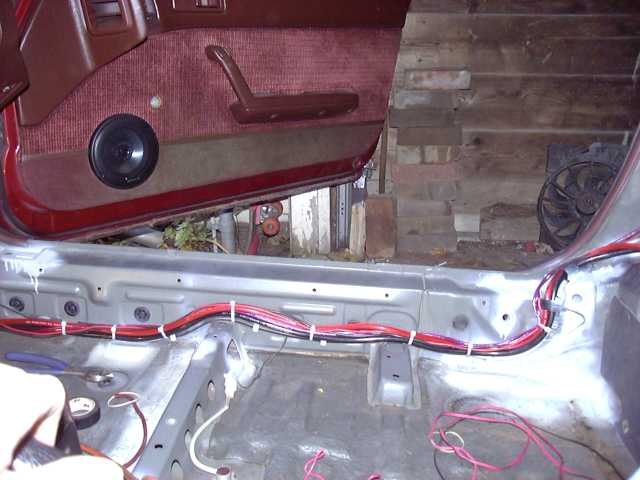
Starting the fuel pump wiring at the pump. I'm going to be crucified for not using sealant-filled heat shrink, but I honestly just ran out. Next time I am in that area, I will correct my sloppy work.
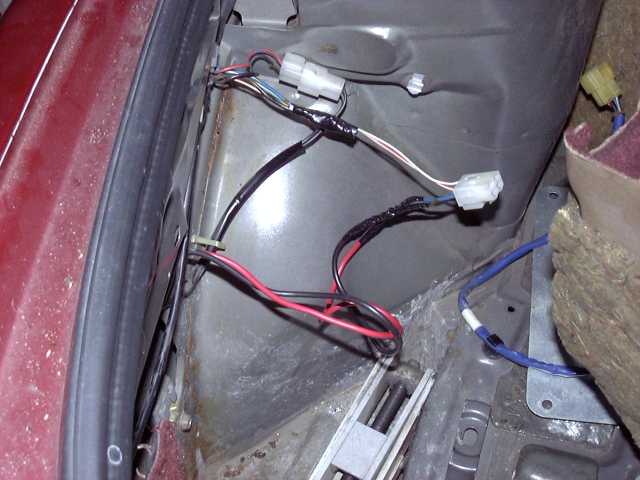
And the fuel pump wiring is finished and tied off. Also notice that the harness plug has also been taped. I've seen these break, so any little bit of extra strength is a good thing in my books.
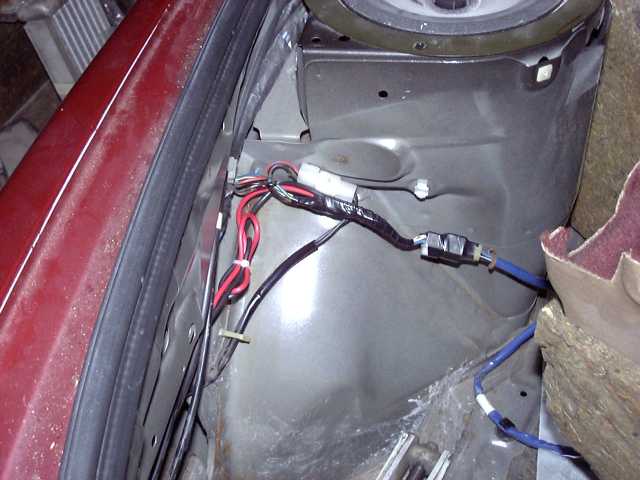
One of the things that really bothers me when people do electrical work is sloppiness. There is absolutely no excuse for bringing cables through unprotected firewall connections. These are battery bulkhead connectors. They provide a pass through that is safe, clean and sanitary. The solid brass bolt in the middle is insulated by a plastic insulator, which screws into the hole and is secured on the other side with a nut. A stud on each end is then provided to make the electrical connection. Not only is this a highly safe and reliable way to pass thick cables through bulkheads, but it also provides a distribution point in the engine bay. From the ground, I can run a thick ground to the engine and the front of the body. From the +12V, a thick wire can go to the starter directly, and then another to the fuse box (and from there, ignition, e-fan, etc.). In this case, the alternator becomes part of the engine harness, which then connects to the battery which is now located inside the car. The disadvantage of these passthroughs is that they are a nightmare to install if the dash is in place. You can see how I had to drill out a stud from the engine side that served to hold the stock dash wiring harness in place. This was done for clearance. The stud has since been welded back into place.
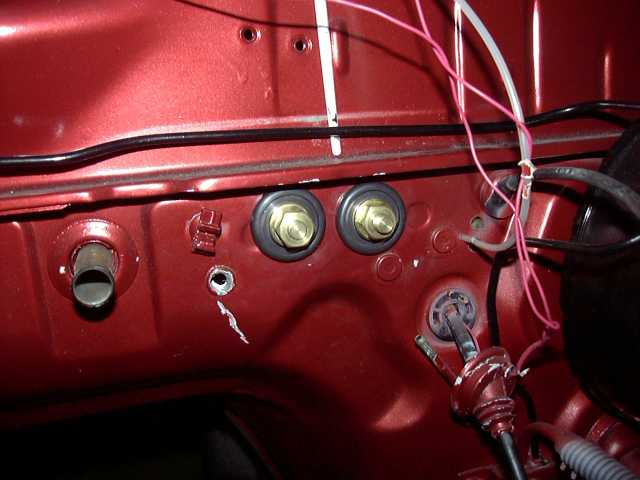
Back inside, here are the finished engine accessories. Intake manifold, water pump and housing, mounts, EGR blockoff, etc.
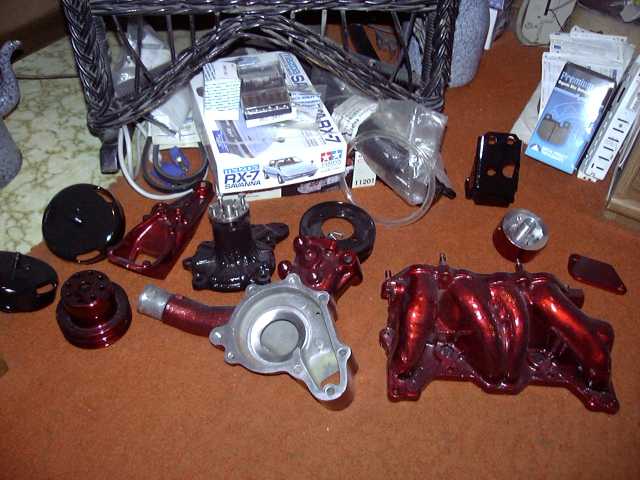
With the engine outside, some mockup was done to make sure everything still fit. These next few pictures provide a great view of the manifold on it's spacer, and how little clearance there actually is between the turbo and lower intake.
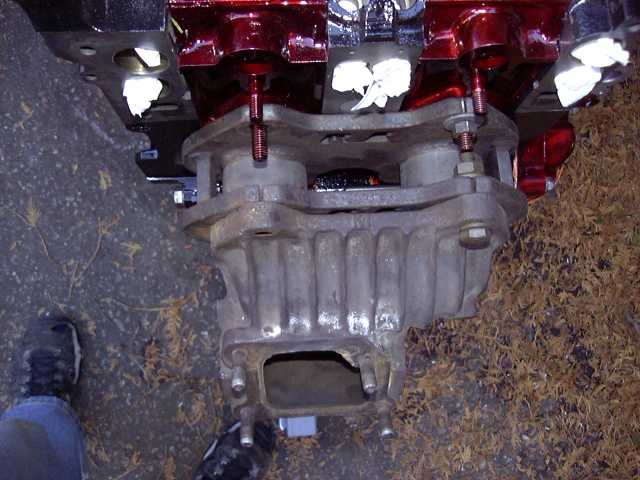
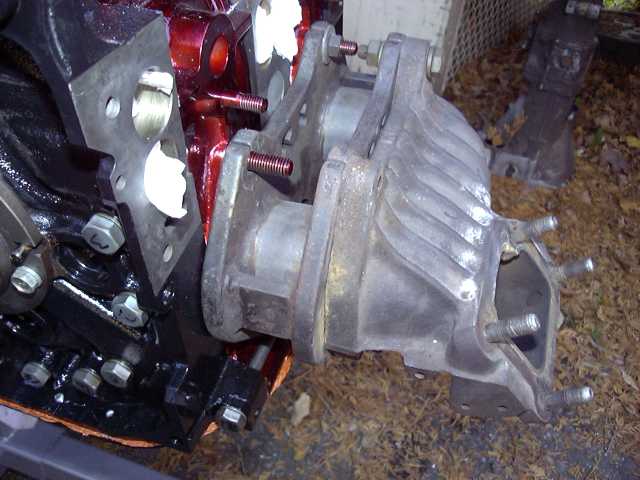
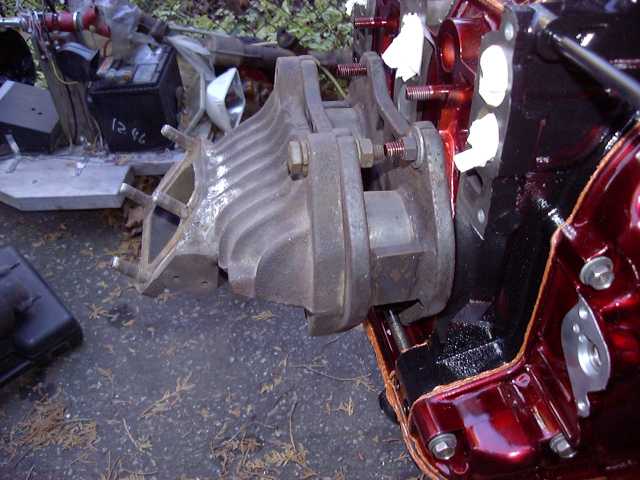

Some great shots of the turbo and lower intake.
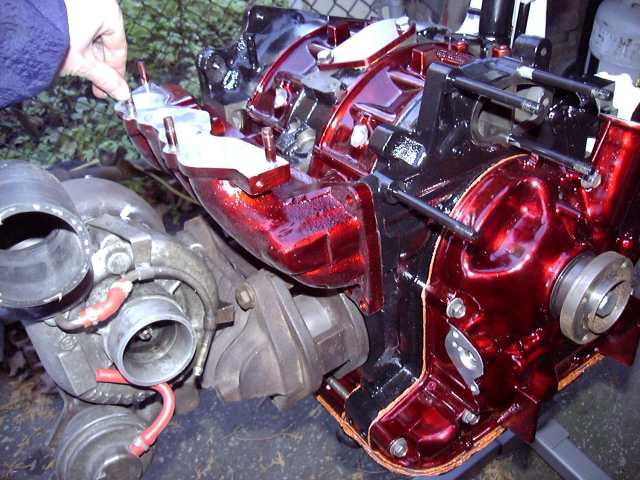
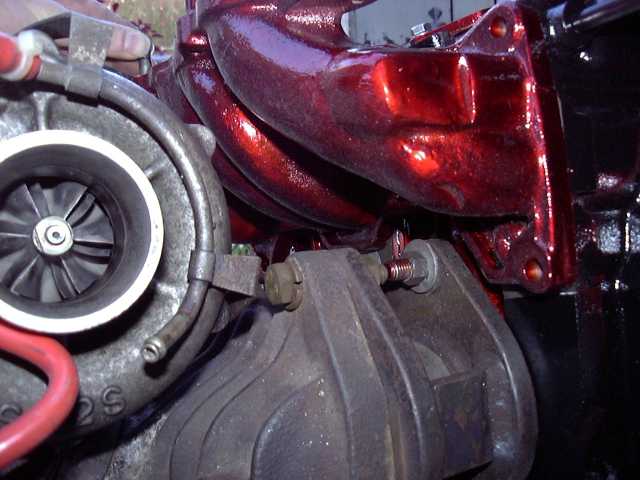
About this time, the Microtech LT-8s arrived in the mail. Shown in the picture is the wiring harness, ECU, vacuum line, relay, instructions and of course the ever important sticker.
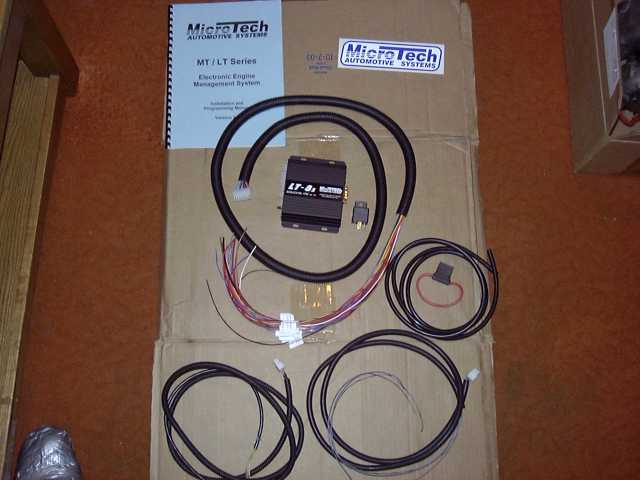
Time for a little more wastegate porting. Some of you might recognize these pictures. Here are the stones I used.
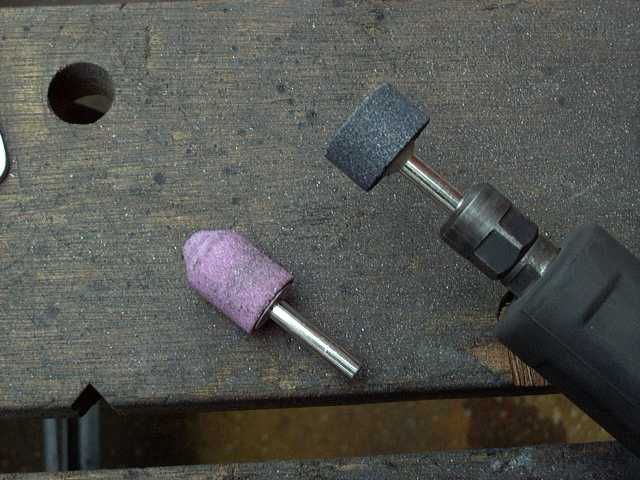
Widening the orifice...
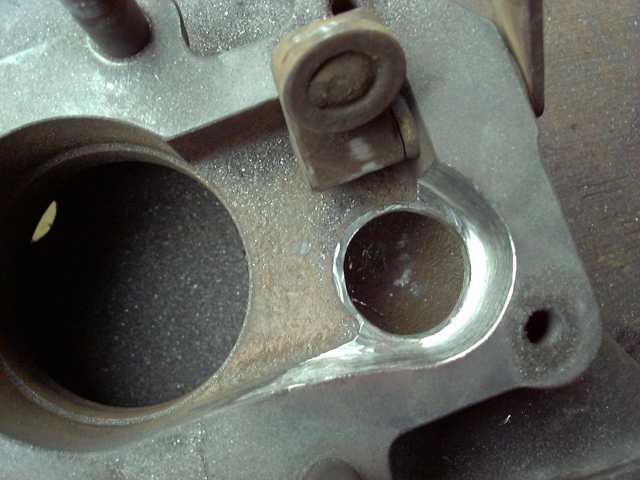
Here's a good shot of the new wastegate passage. It's about twice as large as stock.
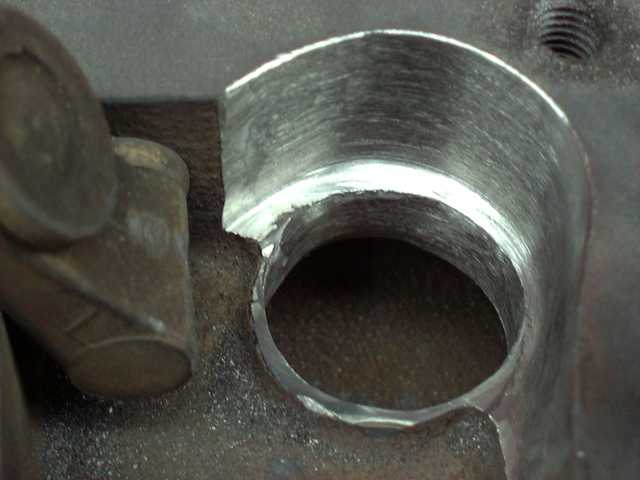
Test fitting the new flapper door.
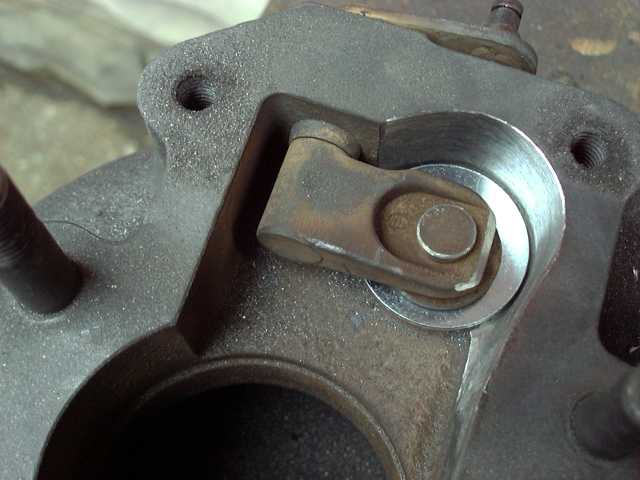
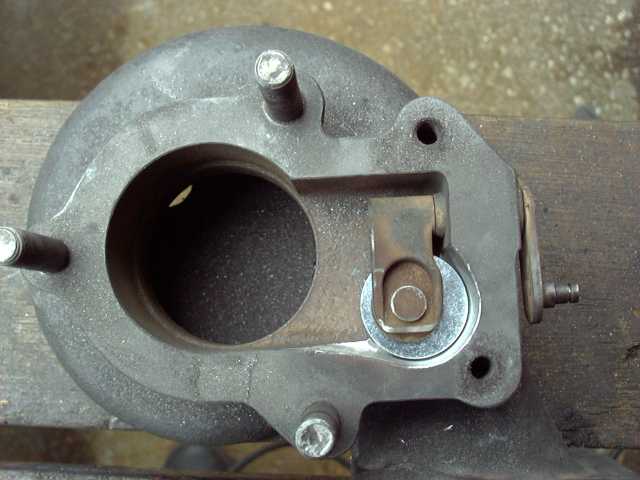
Here's the new flapper door. Two flat washers were simply welded together. The welds were then ground down, and the two washers became as one.
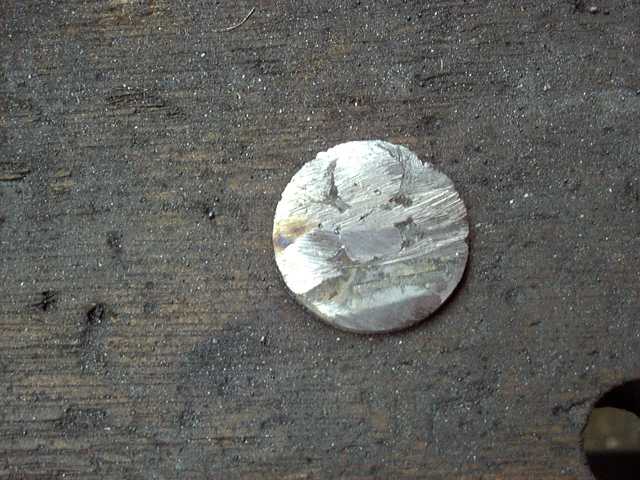
Some shots of the new flapper welded in place.
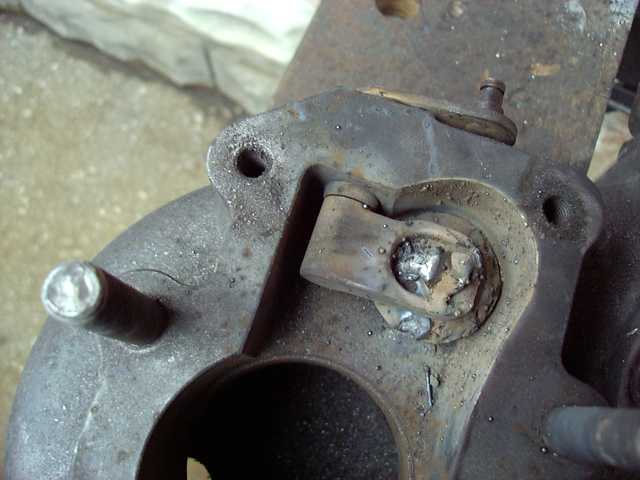
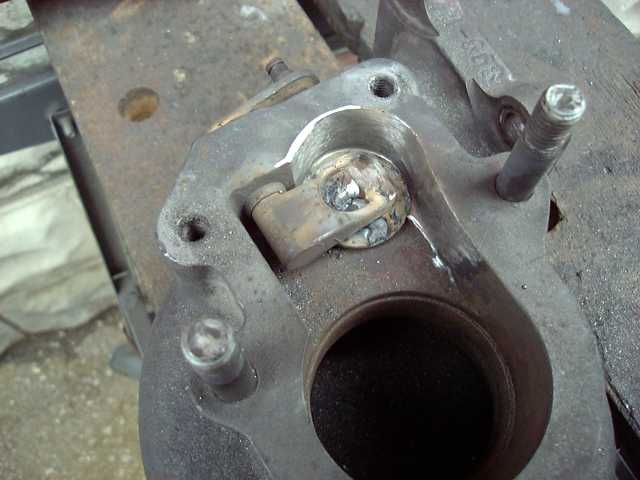
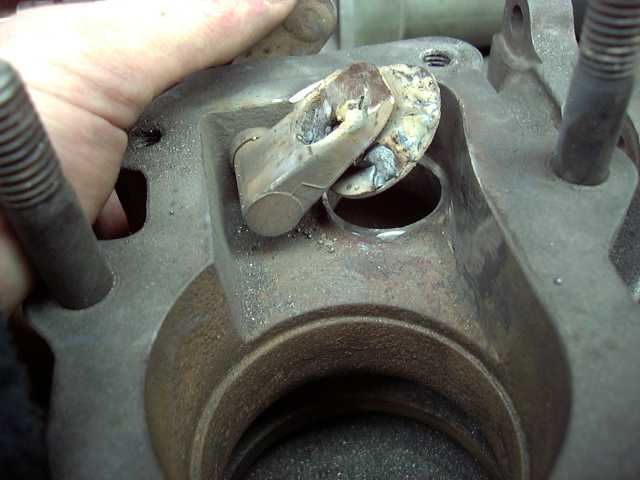
While I'm at it, I figured I would finish porting the exhaust runners. These are not massively ported, since if you make the center divider too thin, it will easily crack (more then it already has).
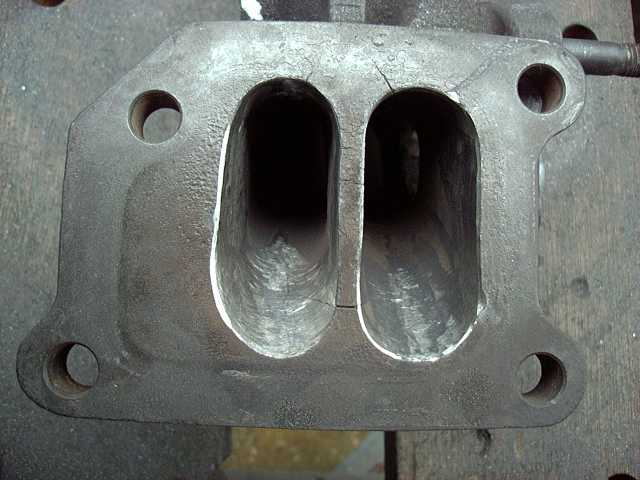
Since I am making a new upper intake for this engine, I needed some flanges cut. I decided to have them done by a machine shop to save some time. So all that was necessary was to design the flange in CAD, and send it to the shop. They cut it out of 8MM steel with a water jet machine. I had a bunch done, so I can experiment with different intakes.
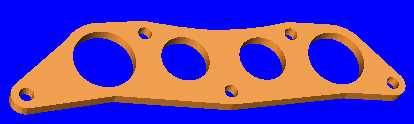
More work on that damn oil pan. I've never been happy with my original turbo drain solution (3/8" 90 degree plumbing elbow). There's nothing fundamentally wrong with it, but there are more elegant ways of accomplishing the task. So I decided to remove the oil drain, and weld on a straight 1/2" NPT pipe union. This would provide a perfect location, that was not in the way of the engine mount like the old drain.
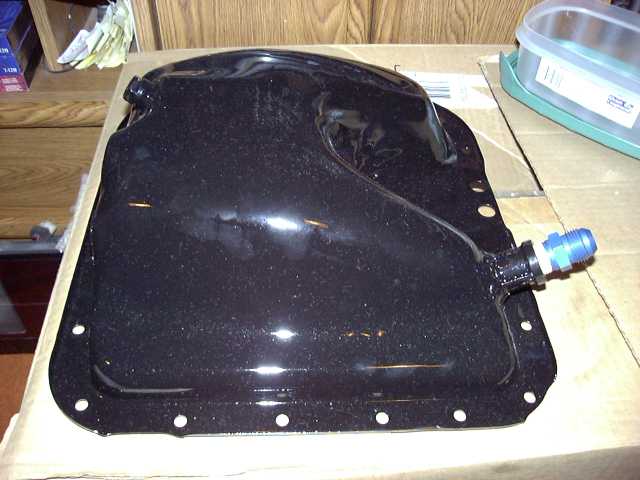
Sometimes, the best laid plans of mice and men just don't work out. I purchased a fancy billet aluminum T4 style oil drain flange from ATP Turbo with the intention of going all braided stainless/AN from the turbo to the pan. Unfortunately, it didn't fit. The flange met up with the holes correctly, but the stock turbo simply doesn't provide enough space between the center section and exhaust flange for any kind of fancy fitting. So I am stuck with the stock drain until I upgrade the turbo. Knowing this, I still wanted the setup to be as reliable and leak proof as possible (I had multiple failures with my old rubber hose). Once again hitting the plumbing isle at Home Depot, I found a 1/2" NPT copper sweat threaded fitting. This was brazed into the cut-off end of the stock drain tube.
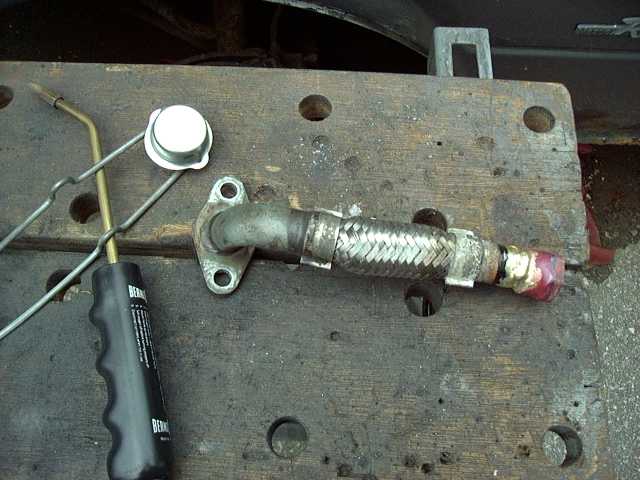
From the brazed fitting, a 1/2" NPT to -10 AN 90 degree fitting was used, and the rest was plumbed in -10 AN and braided stainless. This will never leak. When I upgrade the turbo, the line will be remade to match the new (much more spacious) center section.
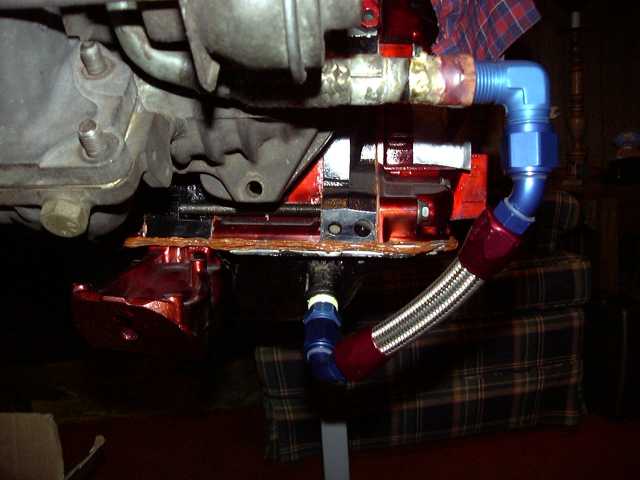
Finally, here are the flanges back from the machine shop. The water jet did an excellent job. I also had some throttle body flanges cut for the stock throttle body, even though I won't be using it.
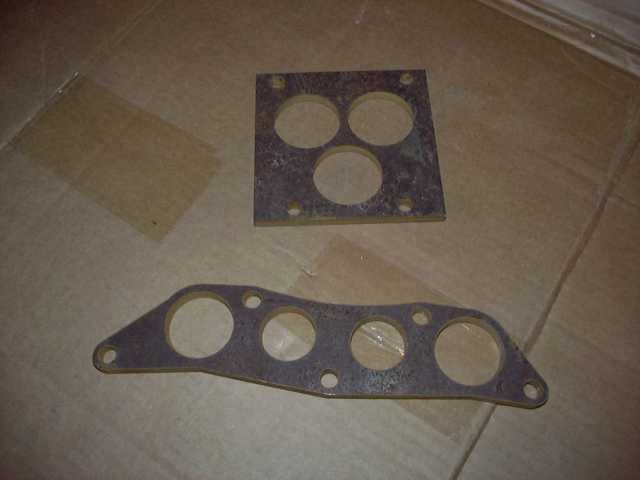
So there you have it. This pretty much brings us up to this weekend. If the weather holds out, the final assembly of the engine (turbo, manifolds, water pump, MOP, flywheel, clutch, etc.) will take place and it will actually be installed in the car. This is a huge milestone, since it means that now I have the location of everything, so fabrication of the upper intake can start, as well as all the wiring, plumbing, etc. I expect things to progress quickly in the engine bay at this point. Now, I can turn my thinking powers to the interior. The seats are heading out to upholstery, and I'm going to tackle the headliner myself. Soon, new carpets will be ordered... |
|
cirvin
Nobel Prize Winner
    
USA
1542 Posts |
Posted - Jun 02 2005 : 7:05:33 PM
|
Wow, I knew you where doing alot to your car, but I was unaware that you had gone all into the cab!
Looks nice, can't wait to see this thing done and running!
http://daxter12.topcities.com <Updated 5/27/05 |
 |
|
Kale
Nobel Prize Winner
    
Canada
795 Posts |
Posted - Jun 02 2005 : 10:57:49 PM
|
Where's the flux capacitor? 
|
 |
|
Aaron Cake
Administrator
    
Canada
6718 Posts |
Posted - Jun 03 2005 : 09:41:34 AM
|
The interior is pretty ratty after almost 20 years on the road. While it is complete, there is some cracked trim and some of the maroon has faded to an odd shade of green. So it's all getting replaced. And since I have my choice of upholstry, I figured I would modernize it a little and bring out the black accents.
As for the flux capacitor, there's no need when you have a GT35R turbo under the hood. That compressor is capable of flowing enough air to make ~650 HP! Not that I'll be taking advantage of that, but it's nice to know it's there...
|
 |
|
Kale
Nobel Prize Winner
    
Canada
795 Posts |
Posted - Jun 03 2005 : 4:09:08 PM
|
quote:
That compressor is capable of flowing enough air to make ~650 HP! Not that I'll be taking advantage of that, but it's nice to know it's there...
What about Pneumatic accessories using the extra pressure? But then, what would you hook up that's pneumatic? Emergency tire air reserve?
|
 |
|
Aaron Cake
Administrator
    
Canada
6718 Posts |
Posted - Jun 05 2005 : 10:12:16 AM
|
Short answer: no. That's not how things work. 
|
 |
|
blah
Apprentice
  
Australia
75 Posts |
Posted - Jun 05 2005 : 5:48:42 PM
|
Wow Aaron you have done a lot of nice work, looking good.
|
 |
|
cirvin
Nobel Prize Winner
    
USA
1542 Posts |
Posted - Jun 05 2005 : 9:08:19 PM
|
Why name it project Tina?
Please say you will drag race this thing, you have 650HP, you must use it!
http://daxter12.topcities.com <Updated 5/27/05
Edited by - cirvin on Jun 05 2005 9:08:53 PM |
 |
|
Aaron Cake
Administrator
    
Canada
6718 Posts |
Posted - Jun 06 2005 : 09:34:51 AM
|
The name "Project Tina" actually has meaning...But first, a little bit of background.
There are basically two types of 2nd gen ('86-'92) RX-7s: the turbo and the naturally aspriated. The turbo is called the "Turbo II", since in Japan they released a turbo 1st gen ('78-'85) which we never saw here. The naturally aspirated cars are by far the most common, and are referred to as "NA". Turbo II is often abbreviated to "TII".
So, years ago when I originally turbocharged my NA car, it needed a name. It was not a Turbo II, but it was certainly not an NA. A RX-7 Forum member by the name of Rxcetra gave it the name "TIINA" by combining TII and NA. I shortened it to "Tina", and the name stuck. Thus, this major project is the 2nd phase of Project Tina. The third phase will take place when this engine pops, and since it's the 3rd phase, the car is getting the 3 rotor...
As for the track, the car will NOT have 650 HP. I am shooting for around 400 HP at the wheels. It will certainly see the track on a regular basis, as I am usually at the 1/4 mile nearly every Friday night. I also autocross, and am hoping to do some minor road racing (though the cost is just HUGE).
|
 |
|
Kale
Nobel Prize Winner
    
Canada
795 Posts |
Posted - Jun 07 2005 : 10:49:51 PM
|
If you ever get some video I'd love to see some clips of you burning rubber in this manned missile of yours. How will she handle? Re; Pressure So the turbo precompresses the air going into the engine, but there's no way to tap into excess? Or am I totally lost about this as I think I am? You say it produces boost for operation up to 650hp, although you're not going to use all of it? I know very little about engines, and even less about rotary, outside of basic operational concepts. BTW, I've heard that some prop aircraft use rotary engines. Do you happen to know of any aircraft names that use rotary engines? Just curious...
|
 |
|
Aaron Cake
Administrator
    
Canada
6718 Posts |
Posted - Jun 08 2005 : 09:18:06 AM
|
Once the car is on the road and broken in, there will certainly be a lot of video. I'm trying to get more and more video of things, since it's becoming a lot easier to post large videos on the website (more people with broadband). This weekend I'll be at an autocross with the Insight, so I'm currently trying to figure out an easy way to mount a camera in the car that will still pass the track's safety...
Boost produced by a turbocharger is dependant on the amount of exhaust gas flow. This is either mechanically controlled (vacuum controlled wastegate with an appropriate spring), electronically controlled (electronic boost controller running a solenoid) or controlled by the right foot...In simple terms, overboosting the engine (creating boost pressures that the fuel system or engine can't handle) will blow it up. Even if you could tap that excess air pressure, what could you do with it? It's much too low to run most air "accessories", and you won't have enough flow to do anything else useful unless you radically oversize the compressor...In which case the enigne won't be able to spool it...
|
 |
|
Kale
Nobel Prize Winner
    
Canada
795 Posts |
Posted - Jun 08 2005 : 2:47:25 PM
|
Ah! Thanks for clearing that up. What is your control system? Mechanical, electrical, or foot? I'm guessing mechanical from your photos?
|
 |
|
Aaron Cake
Administrator
    
Canada
6718 Posts |
Posted - Jun 09 2005 : 09:13:13 AM
|
At the moment, strictly mechanical. The wastegate actuator is plumbed directly into the output of the turbocharger. So boost pressure is primarily set by the spring against the wastegate diaphram. That's fine right now. As soon as I upgrade the turbo (after breaking/testing) I will be moving to an electronic control.
|
 |
|
Kale
Nobel Prize Winner
    
Canada
795 Posts |
Posted - Jun 09 2005 : 11:49:18 AM
|
In an electronic system what sort of sensor would you use to measure the pressure? What sort of feedback loop would you use to control the input valve?
|
 |
|
Aaron Cake
Administrator
    
Canada
6718 Posts |
Posted - Jun 10 2005 : 09:02:04 AM
|
Just a standard pressure sensor. Almost all EFI equipped cars have a pressure sensor in the intake manifold so that the computer can keep track of engine load. Electronic boost controllers use a similar sensor, but usually with a wider range. A little bit of microcontroller magic in the box itself, and a PWM signal is output to a boost duty solenoid. It's pretty simple stuff, but the good electronic controllers can spool a turbo very quickly, have programmable boost levels based on RPM and gear, etc.
|
 |
|
Kale
Nobel Prize Winner
    
Canada
795 Posts |
Posted - Jun 13 2005 : 2:16:00 PM
|
quote:
Just a standard pressure sensor. Almost all EFI equipped cars have a pressure sensor in the intake manifold so that the computer can keep track of engine load.
So as the load on the engine goes up, what happens to the pressure? I would guess it would start to drop because the engine speed (thus air draw) goes down? So then pressing on the gas petal opens up the throttle allowing more air in (in a NA engine) and bringing your RPMs back up?
quote: Electronic boost controllers use a similar sensor, but usually with a wider range. A little bit of microcontroller magic in the box itself, and a PWM signal is output to a boost duty solenoid.
The 'microcontroller magic' is probably a PI or PID control loop. These sorts of algorithms can be very 'tweakable'. I have lots of fun playing around with PID servo controllers in the lab. Changing the 'weights' of the various amplification stages in the control loop can make it do all sorts of entertaining things...
quote:
It's pretty simple stuff, but the good electronic controllers can spool a turbo very quickly, have programmable boost levels based on RPM and gear, etc.
The fun with rapid response systems is to make sure they stay stable. I accidentally had a linear servo motor stage (driven with a big speaker coil and plunger) hammering back and forth like the bolt on an SMG. Not a pretty sound, and kinda hard on the equipment. Luckily the kill switch was close at hand.
|
 |
|
Topic  |
|
|
|